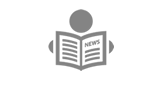
By Alvin A. MINGLE
In the architecture of today’s evolving global marketplace, procurement is no longer just a transactional function; it has evolved into a strategic operation with the potential to drive organizational growth, profitability and sustainability. Supplier development continues to play a pivotal role in achieving this, particularly in the Ghanaian procurement space.
With increasing awareness of issues such as sustainability, human rights, and ethical sourcing, Ghanaian organizations must adopt a more strategic and intentional approach toward developing their supplier base to align with specific organizational goals and meet international standards.
This article explores the importance of supplier development, the need for strategic alignment with broader organizational goals, and the critical support structures that should be in place to enhance supplier capacity, especially in the oil and gas industry in Ghana.
The importance of strategic supplier development
Supplier development refers to the process of working collaboratively with suppliers to improve their performance and capabilities to meet the present and future needs of the procuring organization. In the context of Ghana, supplier development is crucial for the growth of local industries, fostering innovation, and ensuring quality. However, to fully leverage the potential of supplier development, organizations must adopt a strategic perspective.
A strategic approach to supplier development goes beyond merely assessing cost and quality, as is common in the Ghanaian procurement space, where companies often get three quotes and select one. It requires a holistic view that incorporates the organization’s broader goals, such as sustainability, ethical sourcing, and social responsibility.
Organizations should view their suppliers as extensions of themselves. This means ensuring that the values, practices, and supply chains of these suppliers align with the company’s mission and vision. For example, if an organization emphasizes sustainability, it must ensure that its suppliers use sustainable practices in the sourcing and processing of raw materials.
In Ghana’s oil and gas industry, companies such as Tullow Oil have taken strategic steps to develop local suppliers. Through the Petroleum Commission’s “Local Content and Participation” regulations, oil and gas companies are required to prioritize Ghanaian suppliers, ensuring that local businesses are integrated into the supply chain management systems of these multinational oil companies.
This includes providing training and capacity-building programs to local suppliers in areas such as safety, technical proficiency, and adherence to environmental standards.
Tullow Oil, for instance, has partnered with local companies to source products, ensuring that suppliers follow environmentally friendly practices and align with the company’s sustainability goals. Additionally, the firm actively works to reduce its carbon footprint, expecting its suppliers to follow suit by reducing emissions during exploration, drilling, and transportation processes.
This clearly demonstrates an organization with an interest in developing suppliers to meet not only their needs but also to fit into the broader organizational goals.
Aligning supplier base with broader organizational goals
One of the challenges in Ghanaian procurement is the lack of alignment between organizational goals and supplier capabilities. Many organizations focus primarily on short-term gains eg cost savings, often ignoring whether the supplier’s practices support long-term objectives such as sustainability or year-round availability of goods and services. However, procurement professionals must be more deliberate in selecting suppliers whose practices and values align with the organization’s aspirations.
- Sustainability and environmental goals:
Many companies today have made commitments to green and sustainable practices. Organizations must evaluate whether their suppliers are adopting environmentally friendly sourcing, minimizing waste, reducing carbon emissions, and using renewable energy sources.
Even though in the Ghanaian context this might seem theoretical, there is a deliberate need to ensure that these efforts are made, especially in light of the numerous pollutants affecting our forest reserves and water bodies.
This is particularly important in sectors like manufacturing, mining, agriculture, and energy, where the environmental impact can be significant. A supplier using unsustainable raw materials could compromise the company’s overall sustainability goals.
- Human rights and ethical sourcing:
The global focus on human rights issues, particularly in supply chains, is a critical consideration for Ghanaian organizations. Ensuring that suppliers uphold human rights standards, avoid exploitative labor practices, and contribute positively to local communities is essential. Issues such as child labor, forced labor, and unsafe working conditions in the supply chain must be carefully monitored.
The government of Ghana and various NGOs are increasingly emphasizing child trafficking, especially in industries like cocoa and fishing. Organizations must ensure that their suppliers do not engage in such practices.
By strategically developing suppliers that adhere to ethical standards through training and monitoring, organizations can reduce reputational risk, improve brand image, and contribute to broader social impact goals.
Supporting suppliers to enhance capacity and improve performance
For many Ghanaian suppliers, especially small and medium-sized enterprises (SMEs), there is a significant capacity gap. These suppliers may not have the requisite skills, technology, or resources needed to meet the expectations of large organizations, particularly those with global standards.
Thus, organizations must take an active role in developing their suppliers. Once a gap is identified, using strategic measures such as incorporating training and making funds available for the purchase of state-of-the-art facilities not only helps suppliers improve but also enables them to serve the organization better.
This also fits into an organization’s corporate social responsibility by valuing their suppliers, who are members of society, and by extension, creating more jobs.
- Training and capacity building:
Organizations can support supplier development through effective training and capacity-building initiatives. Training on sustainability, quality assurance and control, health and safety standards, and ethical sourcing practices can help suppliers improve their operations. Organizations can also provide technical assistance in areas such as process optimization, technology adoption, and financial management, which will ultimately benefit both parties through improved operations. - Access to finance and resources:
Many suppliers, particularly SMEs, struggle with access to finance. In Ghana, this is often not necessarily a capacity issue but a limitation in the ability to raise money for expansion to meet supply demands and fulfill orders. - This hampers their ability to invest in new technology or expand their operations. Larger organizations can work with financial institutions or set up supplier financing programs that offer favorable terms to their suppliers. This ensures that suppliers have the resources to meet growing demand while adhering to improved standards.
- Collaboration and long-term partnerships:
Organizations should foster collaborative, long-term partnerships with their suppliers. This involves moving away from transactional relationships to a more partnership-based approach, where both parties work towards mutual growth and success. By offering long-term contracts and guaranteeing business, organizations can help suppliers invest in improvements that benefit both parties.
The need for a clear supplier development plan and structure
To effectively develop suppliers to meet organizational standards, there must be a clear supplier development plan and structure. This should outline the objectives, key performance indicators (KPIs), and steps necessary for improving supplier performance.
These plans should be included in supply chain management handbooks and documents. For instance, one of the top-performing organizations bases its selection of suppliers on price, capacity, and willingness to grow alongside the company.
- Supplier audits and evaluations:
Regular supplier audits and evaluations should be conducted to assess compliance with the organization’s ethical, environmental, and performance standards. This goes beyond random quality assurance and control practices. These deliberate, goal-oriented checks are conducted periodically to measure performance. Such audits will help in identifying areas for improvement and ensuring that suppliers consistently align with the company’s broader goals. - Supplier incentive programmes:
Organizations should also consider developing supplier incentive programs to reward suppliers who exceed expectations. For instance, suppliers that demonstrate innovation in sustainability or improve their capacity to meet higher quality standards can be rewarded with additional business, financial bonuses, or public recognition. - Cross-functional collaboration:
Lastly, supplier development should not be the responsibility of the procurement department alone. Cross-functional teams involving departments such as quality control, sustainability, and finance should work together to develop and implement supplier development strategies. This ensures that supplier development is integrated across the organization, reflecting a unified approach to achieving broader goals.
Conclusion
In the Ghanaian procurement landscape, supplier development is an essential strategy, which can no longer be ignored, for organizations to enhance their competitiveness and align with global international standards. By being strategic, intentional, and collaborative, organizations can not only improve supplier performance but also ensure that their suppliers contribute positively to broader goals such as sustainability, ethical sourcing, and social responsibility.
To achieve this, organizations must put in place the necessary structures, including capacity-building initiatives, financing options, and clear development plans, to support suppliers on this journey. In doing so, Ghanaian businesses will not only strengthen their supply chains and continually improve the bottom lines, but also position themselves as leaders in ethical and sustainable procurement practices.
>>>the writer is a Senior Managing Partner, Fitzgerald Bassey Consultancy Limited
The post Strategic supplier development in procurement: aligning with broader organizational goals appeared first on The Business & Financial Times.
Read Full Story
Facebook
Twitter
Pinterest
Instagram
Google+
YouTube
LinkedIn
RSS